Ich bin Jan-Michael Adrian, 27, und Chemikant bei Grace in Worms. 2014 habe ich hier meine Ausbildung abgeschlossen und in der Abteilung Molekularsiebe und Adsorbents angefangen. Wir sind einer der weltgrößten Produzenten für synthetische Zeolithe: Sie entziehen Gasen, Dämpfen und gelösten Stoffen Feuchtigkeit. Im Fensterrahmen etwa verhindern sie, dass Feuchtigkeit im Scheibenzwischenraum kondensiert.
Ich bediene die großen Chemieanlagen sowohl über das Prozessleitsystem als auch vor Ort, prüfe und schalte Aggregate ein, entnehme Proben und dokumentiere die Arbeitsschritte. Dass ich Chemikant geworden bin, verdanke ich meinem Vater. Er ist auch bei Grace, und ich habe ihn als Kind mit meiner Mutter oft von der Arbeit abgeholt. Dadurch wurde ich neugierig, was in diesem großen Betrieb passiert. Und ich wusste, von dem Beruf lässt sich gut leben. Als Chemikant wirke ich aktiv an der Produktion von Dingen mit, die die Welt braucht.
Die Werkzeuge
Meine Arbeitsutensilien sind ein Sicherheitsmesser, Handy und Schreibzeug, weil es immer etwas zu protokollieren gibt. In der Messwarte erfassen wir die Werte zwar im Computer, aber wir machen auch einen Ausdruck für die Dokumentation.
Die Messwarte
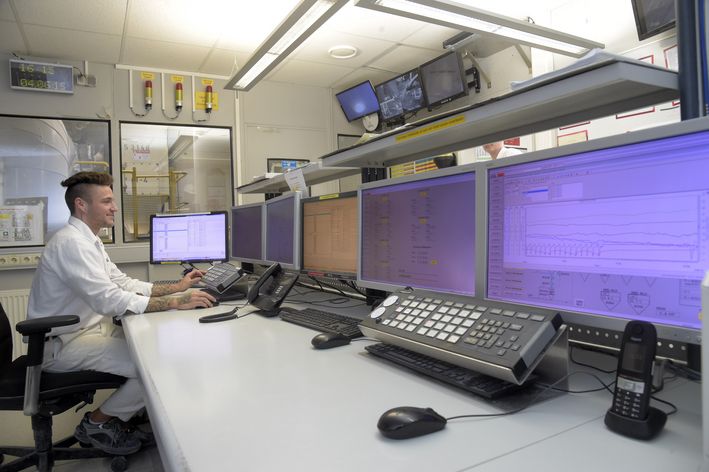
Pro Schicht sind immer mehrere Kollegen anwesend. Wir überwachen von hier sämtliche Prozesse und steuern die Anlagen. Zu Beginn der Schicht schauen wir, was gerade produziert wird und welche Arbeitsschritte dafür notwendig sind. Ebenfalls wichtig ist die Kommunikation mit den Mitarbeitern an der Anlage: Ich kann zum Beispiel über das Prozessleitsystem keine Pumpe einschalten, bevor der Kollege vor Ort grünes Licht gegeben hat, dass alles abgesichert ist.
Granulat und Pulver
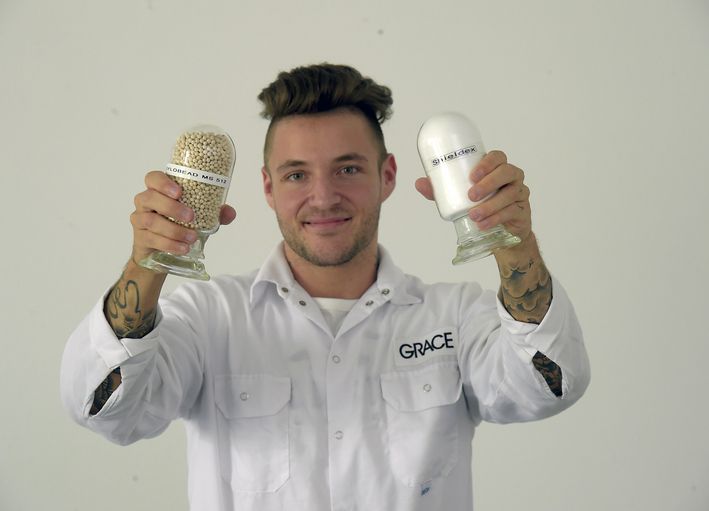
Im Granulierbereich entstehen aus Wasser, Bindemittel und anderen Rohstoffen die Zeolith-Kugeln (links). Der genaue Prozess ist unser Betriebsgeheimnis. Außerdem gibt es noch einen Nassteilbereich für die Produktion von Molekularsiebpulver (rechts): Hier wird die flüssige Suspension zu Partikeln kristallisiert, gefiltert und später getrocknet.
Die Siebmaschinen
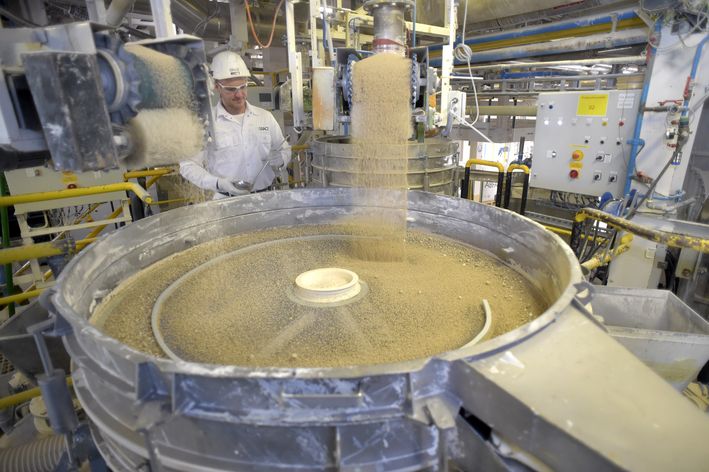
Kugeln, die zu groß für die gewünschte Anwendung sind, werden hier aussortiert. Weil die Siebe vom Rütteln mit der Zeit kleine Risse bekommen können, könnten größere Kugeln durchfallen. Deshalb entnehme ich regelmäßig Proben und prüfe den Durchmesser.
Der Endproduktbereich
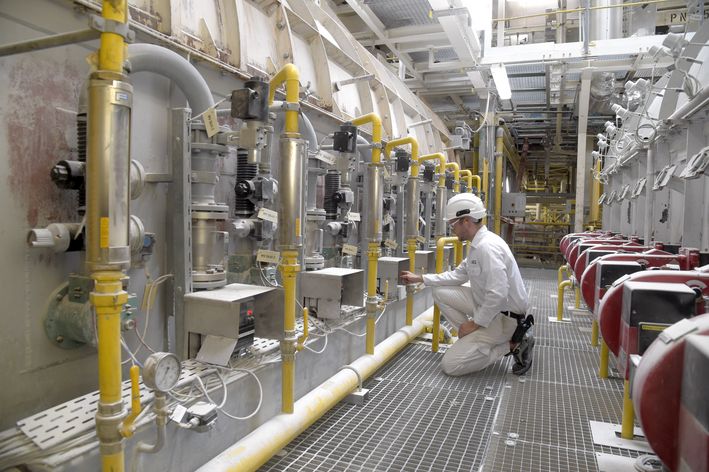
In riesigen Öfen werden die Kugeln auf hohe Temperaturen geheizt und werden so adsorptionsfähig. Ich überprüfe, ob die Brenner die Temperatur in den Öfen aufrechterhalten und schalte einzelne Brenner bei Bedarf ein. Beim Probeziehen kontrolliere ich, ob die Trocknungswerte der Zeolith-Kugeln stimmen, ob das Aufheizen also etwas bewirkt hat. Die fertigen Kugeln fallen in einen Behälter (Foto) und werden per Druckluft zur Abfüllanlage befördert.
Ständige Optimierung
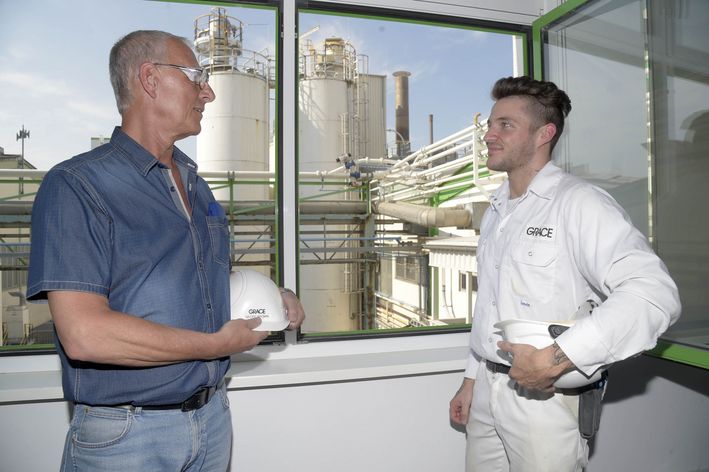
Meinen Chef Geoffrey Brown habe ich als Azubi kennengelernt, als ich einige Monate in der Abteilung Molekularsiebe war. Bei Grace sind wir immer bestrebt, unsere Produkte zu verbessern, Energie zu sparen und die Kosten zu senken. Deshalb bekommt man Schulungen und setzt sich in Gruppen zusammen, um ein bestimmtes Problem zu lösen.