Mein Name ist Patrik Brings, ich bin 47 Jahre alt und Leiter Technische Entwicklung bei Philippine in Lahnstein. Ich habe in Koblenz Maschinenbau studiert und später ein Fernstudium zum Wirtschaftsingenieur draufgesetzt. Bei Philippine bin ich seit 1999, Entwicklungschef wurde ich 2006. Wir sind spezialisiert auf Bauteile aus Schäumen, aus Polyurethan und EPP, also aufgeschäumtem Polypropylen. Zu 80 Prozent liefern wir an Autobauer, etwa Crashpads für Türverkleidungen oder Schäume für Stoßfänger. Sie finden kaum ein deutsches Auto, in dem nichts von Philippine steckt. Und weil beim E-Auto Leichtbau gefragt ist, sind wir auch da gut aufgestellt: Wir fertigen Bauteile für die Zukunft.
Prototypen
Meist kommen Kunden mit fertigen Produkten, meine Mitarbeiter und ich gehen aber auch mit neuen Ideen oder Verfahren auf Kunden zu. Es ist ein Miteinander: Wir unterstützen dabei, dass das beste Bauteil zum besten Preis herauskommt. Hier halten mein Stellvertreter Daniel von Landenberg und ich ein EPP-Frästeil, das für einen Stoßfänger gedacht ist. Diese Frästeile entstehen im Prototypenbau: Der Kunde erhält sie und kann Änderungen daran vornehmen. Sind sie abgenommen, bauen wir die Werkzeuge dafür.
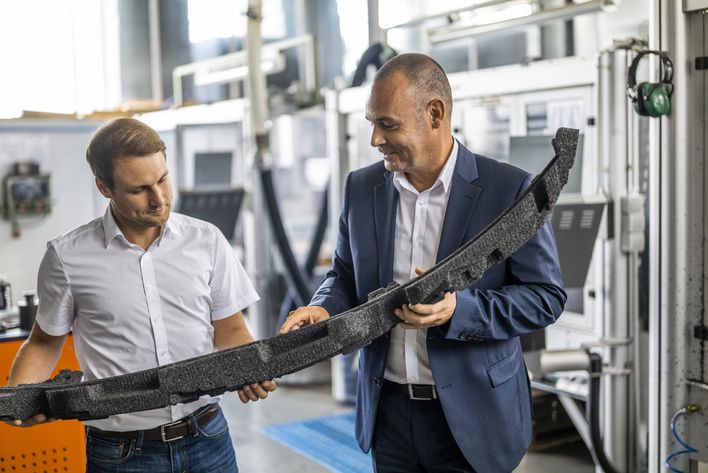
Werkzeugbau
Der eigene Werkzeugbau ist unser großer Vorteil. Zunächst stimmen Entwickler und Konstrukteure die Werkzeuge mit den Kunden ab. Auch ich gebe sie frei, bevor der Bau beginnt: Dann werden die Werkzeuge maschinell aus Aluminium gefräst, am Schluss machen die Werkzeugbauer manuelle Feinarbeiten. Pro Jahr entstehen bis zu 300 Werkzeuge, auf Lager halten wir Tausende.
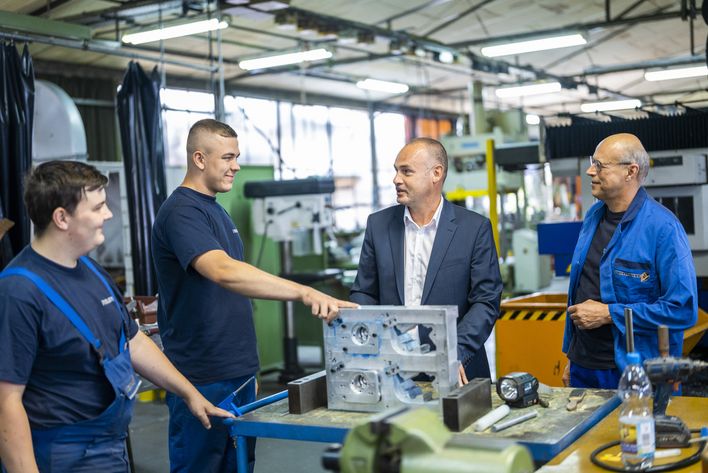
Vertrieb
Unsere Bauteile werden gefragt bleiben, aber wir wollen unabhängiger von der Autoindustrie werden. Deshalb entwickeln, fertigen und verkaufen wir als Phil_Store 24 auf Amazon und Ebay autoferne EPP-Produkte: Thermoboxen, Faszienrollen, Hygienegriffe, damit Sie derzeit keine Griffstangen anfassen müssen, sowie den Reifenschoner Tireplate – meine Idee, um Standplatten zu vermeiden. Direktvertrieb und Online-Marketing waren für uns alle neu. Aber der Erfolg wächst.
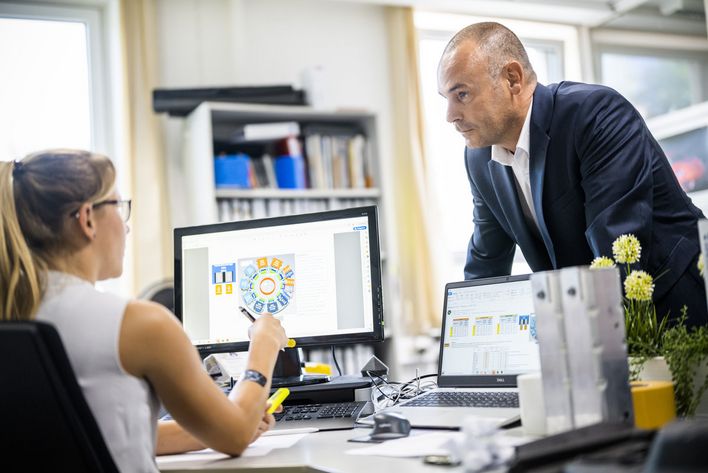
Produktion
In den Anlagen kommen EPP-Kügelchen in die Werkzeuge, dann blasen wir 130 Grad heißen Wasserdampf mit rund vier Bar Druck durch. Der schmilzt die Kügelchen an und verschweißt sie zu Formteilen. Mit jeder Modellgeneration ändern sich die Bauteile, in der Entwicklung wie in der Produktion, die Axel Jansson leitet. Wir produzieren für aktuelle Fahrzeuge, aber auch für die, die in ein, zwei Jahren auf die Straße kommen. Ich sehe Autos, die noch niemand kennt. Ein tolles Gefühl.
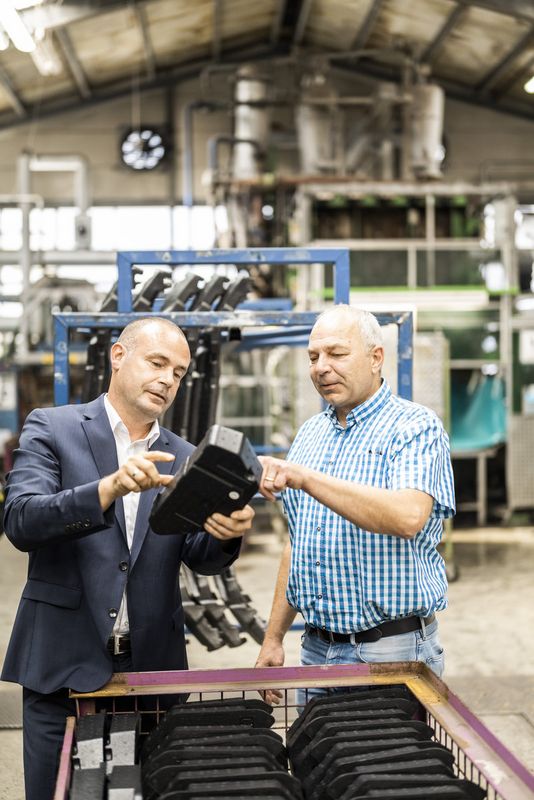
Verantwortung
Wir sind flach organisiert, ich bin für vieles (mit)verantwortlich. Etwa für die 16 Mitarbeiter in Entwicklung, Prototypenbau und Konstruktion sowie die 35 Werkzeugbauer. Im Umgang mit Kollegen musste ich mir viel aneignen: Ich bin ja lange dabei und kenne viele, das Verhältnis zueinander ist oft freundschaftlich. Aber als Vorgesetzter ziehe ich Grenzen. Der unschönste Teil meines Jobs ist der enorme Kostendruck.
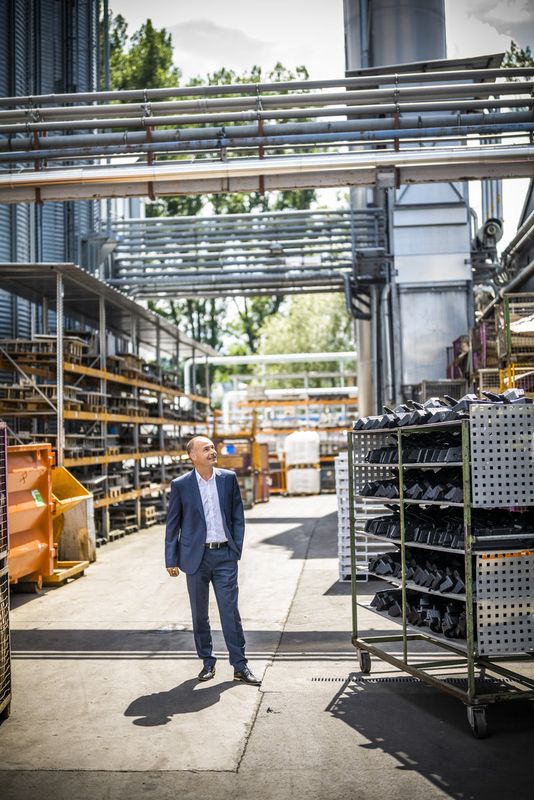