Wer die „kleinste Raffinerie Deutschlands“ besucht, wie sich der Kohlenwasserstoffexperte Haltermann Carless in Speyer nennt, wird neben 50 Meter hohen Destillationstürmen eine riesige Baustelle kaum übersehen können: 2.000 Kubikmeter Beton, 450 Tonnen Stahl und mehr als 13 Kilometer Rohrleitungen werden hier für eine Hydrieranlage verbaut. Die Investition eines mittleren zweistelligen Millionenbetrags durch die Dachgruppe HCS Group soll perfektionieren, wofür Haltermann sich einen Namen gemacht hat: Spezialanbieter für hochwertige Kohlenwasserstoffprodukte zu sein.
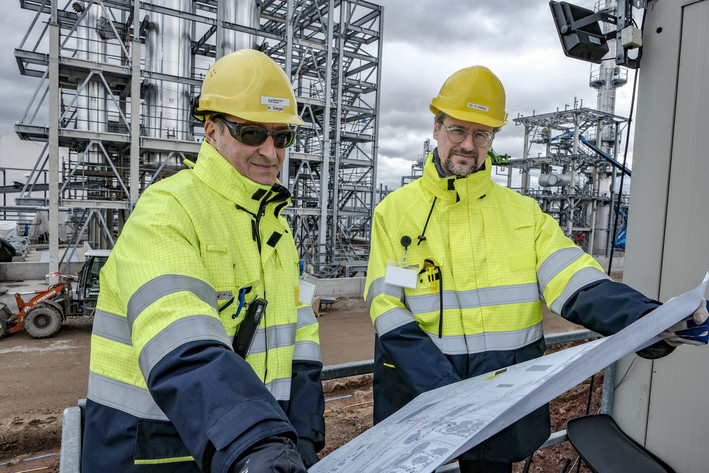
Ein Beispiel sind Druckfarbenöle für den Druck von Geldscheinen. „Der Kunde braucht natürlich immer das genau gleiche Grün. Hier darf es in der Qualität unserer Öle absolut keine Abweichungen geben“, sagt Standortleiter Henning Wartig. Eine weitere Produktgruppe der Speyerer sind die Pentane. „Wie die Druckfarbenöle sind auch sie Kohlenwasserstoffe und entstehen aus Erdöl. Sie gehören zu den leichtesten Komponenten in der Raffinerie und verdampfen sehr schnell, sodass sie gut als Schäumungsmittel für Isolierstoffe funktionieren“, erklärt Wartig.
Hydrieranlage schließt alle unerwünschten Stoffe aus
So gut, dass die Haltermann Carless-Pentane in mindestens jedem zweiten europäischen Kühlschrank eingesetzt seien, und auch die Dämmstoffindustrie beziehe große Mengen für Isolationsmaterialien. Europamarktführer sei man zudem bei hochreinen Lösungsmitteln für die Pharmaindustrie: „Das sind extrem reine Kohlenwasserstoffe, die zum Beispiel in der Synthese und Aufarbeitung der Rohprodukte verwendet werden.“
Aus Raffinerien bezieht Haltermann seine Vorprodukte, die das Unternehmen bislang vor allem in den Destillationskolonnen weiter veredelt. Wartig: „Eine Destillation so zu fahren, dass selbst engste Spezifikationen getroffen werden, erfordert jede Menge Erfahrung. Da haben wir Glück, denn wir haben Mitarbeiter, die 30 Jahre und länger bei uns arbeiten und unsere Anlagen extrem gut kennen.“
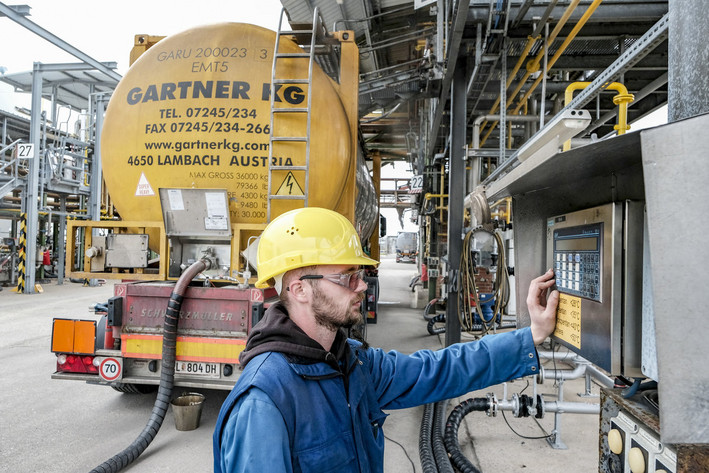
Um gestiegene Kunden- und Marktanforderungen bedienen zu können, kommt ab Mitte 2020 zum Know-how der rund 100 Mitarbeiter die neue Hydrieranlage dazu. „Die Rohware geht dann erst mal durch die Hydrieranlage. All die Stoffe, die zu Verfärbung oder Geruchsbildung neigen, aber auch gesundheitsschädliche Aromaten, sind damit komplett raus. Das heißt, wir haben eine viel höhere Reinheit. Gleichzeitig erlaubt uns die Hydrieranlage, ein breiteres Spektrum an Rohwaren einzusetzen.“ Mit der neuen Anlage müssen die Mitarbeiter auch neues Wissen aufbauen, sagt Chemiker Wartig. Neben zwei neuen Mitarbeitern pro Schicht – die unter anderem für die werkeigene Feuerwehr eingesetzt werden – gibt es Weiterbildungen für den neuen Produktionsprozess.
Hitze, Druck und Wasserstoff steigern Produktreinheit
Wie der funktioniert, erklärt Prozesssicherheitsmanager Hubertus Siegel, 59, der den Bau und die behördlichen Genehmigungsverfahren geleitet hat: „Die Rohware wird bis zu 220 Grad erhitzt, auf 35 Bar unter Druck gebracht und dann über einen Katalysator geleitet. Im zweiten Teil der Anlage, einem großen Tank, werden Zwischenprodukte gesammelt, die in einer weiteren Prozessstufe anschließend wieder in die Hydrierung eingespeist und zu verkaufsfertigen Produkten aufgearbeitet werden. Damit können wir die Ausbeute aus den Rohstoffen maximieren und die Kreislaufwirtschaft optimieren.“
Auf das sich die Kunden laut Standortleiter Wartig nach einer ersten Belieferung mit Mustern, die genau die erwünschten Eigenschaften erfüllen, schon freuen. Auch die weitere Zukunft sieht der 47-Jährige zuversichtlich: „Gerade Dämmstoffe und -schäume werden mit mehr Energieeffizienz im Gebäudebereich immer wichtiger.“
Lernen Sie hier weitere interessante Unternehmen aus Rheinland-Pfalz kennen.